
Blog Posts & White Papers
Stay updated on our advanced tools like apmOptimizer®, fiXtress®, CARE®, and CircuitHawk™, with real-world case studies and success stories.
Blog Posts & White Papers:
CARE

FMECA Report
.jpg)
So, you invested time and effort to conduct a FMECA (Failure Mode, Effects, and Criticality Analysis) for your product / system. You identified potential failure modes, single points of failure, evaluated the potential effects and their severity, and calculated the probability. Finally, you assigned risk to each failure mode based on a criticality matrix.
Now it is time to prepare a report, but what should you include in the report?
The following is also applicable for design FMEA, process FMEA and risk priority number (RPN) analyses.
Why Can Electronic Equipment Fail After a Period of Non-Operation?
.jpg)
Equipment reliability is typically measured by Mean Time Between Failure (MTBF) or failure probability vs. time, where time measures operation hours. When electronic equipment is not used, a user may switch the power off, expecting that next time the device is turned on, it will operate as before. Thus, the failure rate during non-operation is often assumed to be zero. However, in some cases, when a product is not used for a long period of time, it malfunctions when turned back on.
Revolutionizing Healthcare: BQR's Next-Gen Solutions
.png)
In the realm of healthcare systems, ensuring the safety and reliability of medical devices is paramount. At BQR, we understand the critical importance of meeting stringent safety standards and mitigating potential risks. Our suite of innovative products, including CARE® (which facilitates FMEA, FTA analysis, and FMEDA), CircuitHawk™ (for streamlined schematic review and circuit simulation), fiXtress® (for component derating and MTBF prediction), and apmOptimizer® (for reliability analysis and supply chain optimization), is designed to revolutionize the healthcare industry by addressing key challenges faced by medical device manufacturers and healthcare providers.
Integrate Components
De-rating, MTBF and FMECA In The System Engineering Design Process
.png)
Critical products (systems) should be safe, reliable, and easy to maintain. Indeed, RAMS (Reliability, Availability, Maintainability and Safety) related standards state the RAMS analyses that should be conducted in each stage of the system engineering design process (V model), starting from reliability allocation in the initial design stage, and up to detailed failure modes and effects analysis of the complete design, and safety analysis.
Do You Want to Improve Your Reports, or Your Product?

Product design is a complex process that often involves bureaucracy and document preparation to show compliance with regulations and customer requirements.
Reliability, Availability, Maintainability and Safety (RAMS) analyses are standard requirements in industries such as aerospace, defense, rail, automotive, medical, and maritime. A key parameter in these analyses is Reliability.
When test or field data exists, the data can be used for reliability calculation. However, when designing a new product this information is not available, and accelerated life tests are expensive and time consuming.

_edited_edited.png)
Blog Posts & White Papers:
CircuitHawk
Electronic circuits for autonomous vehicles and other mission Critical Systems:
Testing by Simulation to Improve Robustness, Reliability, and Safety
.jpg)
Massive testing is required to verify the quality and reliability of electronic circuits. Furthermore, manual safety verification is needed to comply with various IEC/ISO standards.
BQR introduces a new type of safety and reliability simulation (instead of massive testing and manual analysis) which detects hidden design errors before manufacturing the prototype for testing.
The simulation reduces design cycles thereby saving money and reducing TTM. The product becomes best in class, free of hidden design errors, and improves the manufacturer's reputation.
White Paper:
Automated Schematic Review Driven by
Electrical Stress Analysis
.jpg)
Many engineers spend most of their time working on electronic board development, including functional specifications, design, simulations and testing of the product.
How sure are you that your product is robust and reliable?
Due to market pressure and the lack of tools, hidden design errors remain undetected. Sometimes, it does not take a long time until the customer uncovers some errors. That seriously affects the company’s reputation and incurs financial losses.
White Paper:
Is Your Organization Ready for RAMS Digitization?

In this article, we will introduce a new “Engineering & RAMS Digitalization” system (RAMS-D), which will shorten the time needed to perform RAMS analyses and product qualification testing. This method will ensure robust and reliable products with fast Time to Market. From analyzing the time spent on doing RAMS analyses we found that more than 50% of the time is spent on collecting product data and preparing it for the RAMS analyses.
Revolutionizing Healthcare: BQR's Next-Gen Solutions
.png)
In the realm of healthcare systems, ensuring the safety and reliability of medical devices is paramount. At BQR, we understand the critical importance of meeting stringent safety standards and mitigating potential risks. Our suite of innovative products, including CARE® (which facilitates FMEA, FTA analysis, and FMEDA), CircuitHawk™ (for streamlined schematic review and circuit simulation), fiXtress® (for component derating and MTBF prediction), and apmOptimizer® (for reliability analysis and supply chain optimization), is designed to revolutionize the healthcare industry by addressing key challenges faced by medical device manufacturers and healthcare providers.
.png)
Blog Posts & White Papers:
fiXtress
Integrate Components Derating, MTBF and FMECA in the System Engineering Design Process
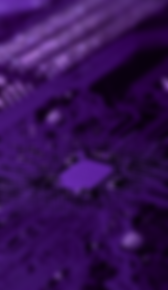.png)
Critical products (systems) should be safe, reliable, and easy to maintain. Indeed, RAMS (Reliability, Availability, Maintainability and Safety) related standards state the RAMS analyses that should be conducted in each stage of the system engineering design process (V model), starting from reliability allocation in the initial design stage, and up to detailed failure modes and effects analysis of the complete design, and safety analysis.
Do you Want to Improve Your Reports, or Your Product?

Product design is a complex process that often involves bureaucracy and document preparation to show compliance with regulations and customer requirements.
Reliability, Availability, Maintainability and Safety (RAMS) analyses are standard requirements in industries such as aerospace, defense, rail, automotive, medical, and maritime. A key parameter in these analyses is Reliability.
When test or field data exists, the data can be used for reliability calculation. However, when designing a new product this information is not available, and accelerated life tests are expensive and time consuming.
Ensuring Optimal PCB Design: The Importance of Early Thermal Analysis

Ensure reliable, efficient PCBs with early thermal analysis! This paper explains why analyzing thermal properties early is crucial for PCB design. By proactively managing heat, you can avoid problems later. We introduce fiXtress Mini Thermal Analysis, a tool that estimates temperature rise and helps identify heat issues before finalizing your PCB layout and component placement.
Stop Guessing, Start Predicting: Boost Your Product Reliability with MTBF Software

Worried about product reliability? Predict it with MTBF!
MTBF (Mean Time Between Failures) is the secret weapon for engineers who want to build products that last. This post dives into what MTBF is, why it matters, and how to use it to your advantage. Plus, learn how BQR's MTBF software can streamline the process and boost your product's reliability!
fiXtress®: Optimizing Design for Safety, Reliability, and Maintainability Across Industries

Imagine a future where cutting-edge technology guarantees the safety and reliability of your car. fiXtress®, a revolutionary AI-powered design software, is making this vision a reality in the automotive industry. This software tackles the challenges of complex car designs, optimizing for safety, reliability, and maintainability. Keep reading to discover how fiXtress® is shaping the future of automotive design.
Why Can Electronic Equipment Fail After a Period of Non-Operation?
.jpg)
Equipment reliability is typically measured by Mean Time Between Failure (MTBF) or failure probability vs. time, where time measures operation hours. When electronic equipment is not used, a user may switch the power off, expecting that next time the device is turned on, it will operate as before. Thus, the failure rate during non-operation is often assumed to be zero. However, in some cases, when a product is not used for a long period of time, it malfunctions when turned back on.
Revolutionizing Healthcare: BQR's Next-Gen Solutions
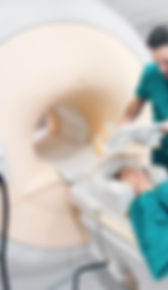.png)
In the realm of healthcare systems, ensuring the safety and reliability of medical devices is paramount. At BQR, we understand the critical importance of meeting stringent safety standards and mitigating potential risks. Our suite of innovative products, including CARE® (which facilitates FMEA, FTA analysis, and FMEDA), CircuitHawk™ (for streamlined schematic review and circuit simulation), fiXtress® (for component derating and MTBF prediction), and apmOptimizer® (for reliability analysis and supply chain optimization), is designed to revolutionize the healthcare industry by addressing key challenges faced by medical device manufacturers and healthcare providers.
Unlocking Efficiency with fiXtress®: Introducing Rapid Stress Assignment®

Are you bogged down by manual stress assignment in your electrical design projects? Imagine a future where this critical step is tackled swiftly, free from the burden of tedious calculations and potential errors. fiXtress® introduces Rapid Stress Assignment, making this vision a reality.
This post dives into how fiXtress® revolutionizes your workflow:
-
Automate calculations for unfinished designs, achieving significant time savings.
-
Foster seamless collaboration with your team on a single project, enhancing efficiency.
-
Empower proactive decision-making with pre-BOM freeze analysis, ensuring a smoother design process.
Derating Analysis for Electronic Components
.png)
Derating analysis: The key to ensuring electronic component reliability.
Struggling to meet MTBF targets? Excessive field returns due to component failure?
Derating analysis can be your secret weapon for designing robust and reliable electronic products.
This blog post explores the critical role of derating analysis in:
-
Maximizing component lifespan
-
Preventing overstress failures
-
Optimizing cost-effectiveness
We'll also introduce fiXtress®, an innovative AI-powered solution that streamlines the derating process, saving you valuable time and resources.
Take control of your electronic design process and ensure long-lasting product performance. Read the full blog post now!
_edited_edited.png)
Blog Posts & White Papers:
apmOptimizer
Life Cycle Cost and Maintenance Optimization During Design:
What is In It for You?
.jpg)
Asset intensive facilities/fleets have high maintenance costs.
Best practice KPI is an annual maintenance cost, which is 3% of the replacement asset value (in most cases the cost is even higher).
Therefore, optimizing the maintenance policy can significantly reduce the asset Life Cycle Cost (LCC).
However, when the asset is already in operation, maintenance optimization options are limited.
Maintenance optimization should be considered during the design phase, when flexibility exists regarding maintenance and operations related decisions (example: installed stand-by items vs. mobile spare parts, repair tiers and supply chains).
Sparing for Availability and Sparing for Confidence – Use for Cloud Computing Services

Cloud computing services, Web hosting companies and Data Centers guarantee high service availability to the users (up to 99.999%). While industry standards exist for tier I – IV data centers, following the standard does not guarantee the required availability. Therefore, reliability and maintenance optimizations are crucial. Standard spare optimization strategies include sparing for confidence (where the goal is to minimize the probability of a stock-out), and cost optimization (where spare and down-time costs are minimized). However, in the case of cloud services a different approach is needed: sparing for availability.
Life Cycle Cost and Maintenance Optimization During Design:
What is In It for You?
.jpg)
Asset intensive facilities/fleets have high maintenance costs.
Best practice KPI is an annual maintenance cost, which is 3% of the replacement asset value (in most cases the cost is even higher).
Therefore, optimizing the maintenance policy can significantly reduce the asset Life Cycle Cost (LCC).
However, when the asset is already in operation, maintenance optimization options are limited.
Maintenance optimization should be considered during the design phase, when flexibility exists regarding maintenance and operations related decisions (example: installed stand-by items vs. mobile spare parts, repair tiers and supply chains).
White Paper: Maintenance of a Drone Fleet

Optimize Drone Fleet Maintenance with apmoptimizer® & Slash Costs by 34%!
This article explores a case study where apmoptimizer®, a leading fleet optimization tool, reduced drone fleet maintenance costs by 34% while increasing availability. Learn how detailed fleet modeling incorporating reliability, maintenance data, and financial factors can improve your operations. This approach is applicable to various fleets beyond drones!